B3-26-34D Stainless Steel 304/316 Brazed heat Exchanger 1HP to 6HP OEM BPHE Plate Type Industrial Heat Exchanger for Chiller
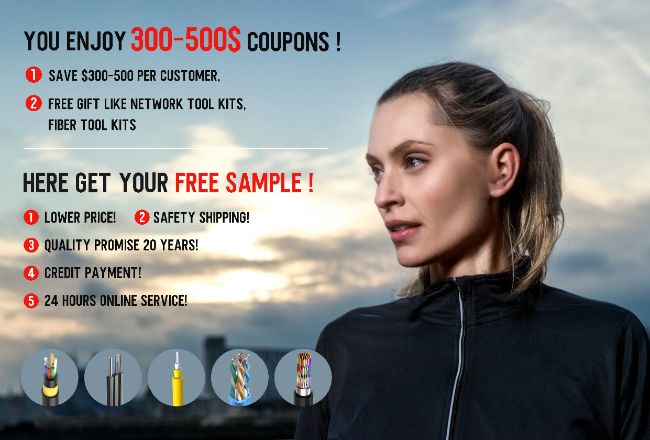
Contact me for free samples and coupons.
Whatsapp:0086 18588475571
Wechat: 0086 18588475571
Skype: sales10@aixton.com
If you have any concern, we provide 24-hour online help.
xType | Heat Exchanger Tube | Application | Refrigeration Parts |
---|---|---|---|
Weight (kg) | 20 | Warranty | 1 Year |
Video Outgoing-inspection | Provided | Achinery Test Report | Provided |
Place Of Origin | Shanghai, China | Brand Name | KUB |
Material | 304/316L | Packing | Wooden Box |
Product Name | Brazed Plate Heat Exchanger | Application | Cooling System |
Refrigerant | R22/410A/407C/R404A/R507 | Horse Power | 3HP |
After-sales Service Provided | Online Support | Keyword | Heat Exchanger |
Original | China | ||
Highlight | 304/316 Brazed heat Exchanger |
B3-26-34D Stainless Steel 304/316 Brazed heat Exchanger 1HP to 5HP OEM BPHE Plate Type Industrial Heat Exchanger for Chiller
Product parameter description
B3-26 series model (N is the number of plates) | |
Single piece heat exchange area (m²) | 0.026 |
Design pressure (MPa) | 3.0/4.5 |
Test pressure (MPa) | 4.5/6.5 |
Thickness of plate package (mm) | 9+2.4N |
Effective heat exchange area (m²) | 0.026(N-2) |
Design temperature (℃) | -100/+200 |
Channel Type | D,X,H |
Optional materials for the board | 304 ,316L |
Maximum number of assembled pieces | 150 |
Maximum interface | DN40 |
Commonly used refrigerant standard operating conditions evaporator selection query table
Product structure
Installation, use and maintenance of brazed plate heat exchangers
Install
1. Plate heat exchangers should be installed vertically, and horizontal or inclined installation will not only cause a significant decrease in the heat exchange efficiency of the heat exchanger, but also increase the capacity for refrigeration
Easy to cause ice formation and blockage in the heat exchanger.
2. Small plate heat exchangers of models B3-014, B3-015, B3-020, and B3-026 (≤ 30 pieces) can be directly installed on pipelines. Large plate heat exchangers of the above models and other larger models should be installed on shock-absorbing plates or fixed with bolts, screws, brackets, etc. If vibration may occur, shock-absorbing connections should be used.
3. Except for special design cases, when connecting the heat exchanger to the system, it should be ensured that the connecting pipes for the inlet and outlet of the hot side medium and the inlet and outlet of the cold side medium are connected in an upward manner
Ensure good convective heat transfer and avoid connection errors.
4. When brazing the plate heat exchanger and pipeline, the contact surface should be wiped clean first, the grease should be removed, and gas acid salt (or silver powder) brazing agent should be brushed with a brush. The copper tube should be inserted into the interface and welded with a silver welding rod containing more than 45% silver. When welding, direct the flame towards the pipe, with a maximum temperature not exceeding 650 ℃, for welding at the same welding point
The time should not be too long. In order to prevent internal oxidation, nitrogen gas needs to be filled inside the heat exchanger for protection.
5:When welding the B3-095 and above large plate heat exchangers with pipelines, a damp cloth should be wrapped around the interface to avoid the heat exchanger being exposed to high temperatures. To limit the heated area, an angle (usually 30 °) should be created at the edge of the pipeline and interface, and TG or MG welding should be used.
Precautions for use and maintenance
1. Anti blockage
If foreign objects or severe scaling enter the channels of the heat exchanger, channel blockage will occur. When used in the evaporator, it will cause icing, and when used in the condenser, it will cause corrosion, which will damage the structure of the heat exchanger and result in internal leakage. Therefore, it is necessary to pay attention to the pressure loss changes of the medium before and after passing through the heat exchanger at all times. If the pressure loss suddenly increases, the machine should be stopped in time for cleaning and maintenance of the heat exchanger. If necessary, a new heat exchanger should be replaced in a timely manner to avoid greater losses.
2. Anti icing
A. Antifreeze should be used when the evaporation temperature approaches the freezing point on the liquid side
B, To prevent the refrigerant from being injected too little and causing the evaporation temperature to be too low, regular cleaning and maintenance should be carried out to prevent ice formation caused by scaling and blockage of the heat exchanger channel. D, Soften water with high hardness to prevent ice formation caused by blockage of heat exchanger channels due to scaling.
E, Install drainage devices and empty the heat exchanger when not in use to prevent freezing inside the heat exchanger due to low ambient temperature
F, Install and use filter screens with holes less than 1 millimeter to prevent filamentous, flocculent, and larger debris from entering the heat exchanger, and to avoid ice formation caused by blockage of the heat exchanger channels
G. Install a water flow switch to ensure a stable water flow before, during, and after the operation of the compressor, to avoid sudden shutdown of the water pump during system operation
H, Install low voltage protection control switch to prevent low suction pressure
1. Install the temperature protection controller after installing the expansion valve, and turn off the compressor when the temperature behind the
3. Anti corrosion
A. To avoid corrosion of the heat exchanger, it is necessary to ensure that the environment in which the heat exchanger is installed and used, as well as the medium used for heat exchange, are non corrosive to stainless steel and copper metals (the content of chloride ions and sulfate ions in the heat exchange medium generally should not exceed 100mg/1).
B, Use a filter with holes less than 1 millimeter to prevent filamentous, flocculent, and larger debris from entering the heat exchanger and causing blockage
C. Clean the heat exchanger promptly when fouling occurs.
D, Ensure the stability of system operation and avoid stress corrosion of heat exchanger plates caused by severe or frequent changes in system pipeline pressure.
E, When the system stops running and remains idle for a long time, the liquid in the heat exchanger should be drained
4. Cleaning
If there is a significant pressure drop during the operation of plate heat exchangers, it means that scale has formed. Generally, oily scale should be cleaned with cleaning agents. If the scale is severe, chemicals that do not damage stainless steel metal and copper metal should be used for 24-hour reverse cleaning (such as 5% concentration phosphoric acid or peroxide acid, formic acid, carboxylic acid, acetic acid, oxalic acid or other organic acids). When cleaning, the flow rate of the cleaning solution should be controlled by a water pump under pressure. The optimal flow rate is 1.5-2 times the flow rate of the original solution. After cleaning, a large amount of clean water should be used to rinse the cleaning solution in the system before starting the system